Find your next role
Showing 2454 results
Sort by:
Water Wastewater Project Manager
Job Title: Water/Wastewater Project ManagerWe are currently seeking a Project Manager to support our Potable Water and Wastewater group in Denver! The Potable Water and Wastewater services covers a broad array of work, including moving projects from conceptual planning through design, financing, permitting, construction, start-up, and operation. So...
Managing Director Forensic Accounting & Investigations
Our client is a prestigious global consulting firm that combines technical, scientific, financial, and strategic expertise to advise clients seeking to realize value and mitigate risk. The firm provides a comprehensive suite of services, enabling clients to navigate complex, contentious, and often catastrophic situations. They are seeking a highly ...
Site/Civil Project Manager
Site/Civil Project Manager - IndianapolisWe are seeking a dedicated and experienced Site/Civil Project Manager to join a top-performing, nationally recognized multidisciplinary engineering firm headquartered in Indianapolis. With a reputation as one of the Top 150 ENR firms and one of the 15 best firms in the Midwest, this organization combines ext...
Elevate your career
Take the first step toward your next opportunity - submit your resume and get started today.
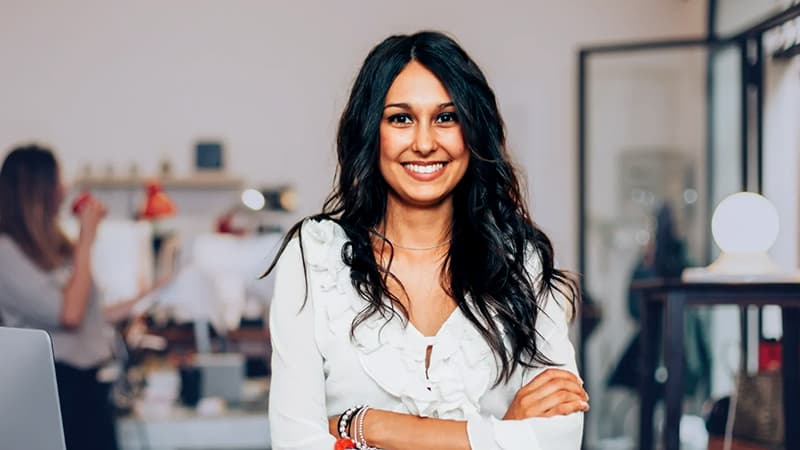
Senior Superintendent Atlanta
Senior Superintendent - Data Center ConstructionWe are seeking an experienced Senior Superintendent to join a dynamic team in Atlanta. This is a permanent position focused on managing Data Center construction projects, particularly within Hyperscale Data Centers. The ideal candidate will bring a wealth of experience in general contracting and a pro...
Field Service Representative
Position OverviewThe Field Service Representative is responsible for the hands-on operation and maintenance of an advanced wastewater treatment facility. This role involves supporting system commissioning, ensuring compliance with water quality standards, and assisting with site tours and customer engagement. The representative will serve as a key ...
Land Development Project Manager Remote
Senior Project Manager - Land Development (Civil/Environmental Engineering)Flexible Location | Remote/Hybrid Options AvailableAre you a seasoned professional passionate about solving complex land development challenges? Do you thrive in dynamic environments where your leadership directly shapes communities and client success? If you're seeking a ro...